ProSonic
Frontloader washers
Frontloader wash cabinets X53 series
Cleaning or pre-washing cylinder heads, among other things, is what the X53 series is known for. Thanks to its maximum load capacity of 700kg and rotating basket up to 1,800mm, you will place the most common objects.
The integrated water tank with heater, ensures an always warm and clean spray bath. By using the circulation water up to a temperature of 70°C adjustable, the machine goes along with the sustainability of your workplace.
Depending on the object and model of the spray washer, position the object one or more times for the most optimal cleaning under 2.5bar.
Are you dealing with objects with hard-to-reach surfaces or hidden rooms? Then also inquire about our ultrasonic baths for immersed cleaning techniques.

L160
Description:
- Made of AISI 304 stainless steel
- Basket diameter Ø1,100mm up to 700kg
- Rotary basket, motorized
- Removable basket on trolley
- Touch screen or remote controlled, Siemens PLC
- Electric heater, temperature adjustable up to 70°C
- Easily adjustable cleaning timer
- Circulating spray cleaning, 450L per minute
- Vapor extraction after cleaning
- Dirty water discharge pump
- Thermal insulation for longer temperature maintenance
- 3 phase N+G, 400V
Optional:
- Blower
- Automatic water and soap refill system
- Oil skimmer with drain connection
- Warm air dry blowing function
- Increasing payload capacity up to 1,500kg
- Rinse function via direct water supply line
- Automatic cleaning programs
- Oil filter (settling tank)
- Hour meter

L190
Description:
- Made of AISI 304 stainless steel
- Basket diameter Ø1,300mm up to 700kg
- Rotary basket, motorized
- Removable basket on trolley
- Touch screen or remote controlled, Siemens PLC
- Electric heater, temperature adjustable up to 70°C
- Easily adjustable cleaning timer
- Circulating spray cleaning, 500L per minute
- Vapor extraction after cleaning
- Dirty water discharge pump
- Thermal insulation for longer temperature maintenance
- 3 phase N+G, 400V
Optional:
- Blower
- Automatic water and soap refill system
- Oil skimmer with drain connection
- Warm air dry blowing function
- Increasing payload capacity up to 1,500kg
- Rinse function via direct water supply line
- Automatic cleaning programs
- Oil filter (settling tank)
- Hour meter

L210
Description:
- Made of AISI 304 stainless steel
- Basket diameter Ø1,300mm up to 700kg
- Rotary basket, motorized
- Removable basket on trolley
- Touch screen or remote controlled, Siemens PLC
- Electric heater, temperature adjustable up to 70°C
- Easily adjustable cleaning timer
- Circulating spray cleaning, 500L per minute
- Vapor extraction after cleaning
- Dirty water discharge pump
- Thermal insulation for longer temperature maintenance
- 3 phase N+G, 400V
Optional:
- Blower
- Automatic water and soap refill system
- Oil skimmer with drain connection
- Warm air dry blowing function
- Increasing payload capacity up to 1,500kg
- Rinse function via direct water supply line
- Automatic cleaning programs
- Oil filter (settling tank)
- Hour meter

L240
Description:
- Made of AISI 304 stainless steel
- Basket diameter Ø1,800mm up to 700kg
- Rotary basket, motorized
- Removable basket on trolley
- Touch screen or remote controlled, Siemens PLC
- Electric heater, temperature adjustable up to 70°C
- Easily adjustable cleaning timer
- Circulating spray cleaning, 550L per minute
- Vapor extraction after cleaning
- Dirty water discharge pump
- Thermal insulation for longer temperature maintenance
- 3 phase N+G, 400V
Optional:
- Blower
- Automatic water and soap refill system
- Oil skimmer with drain connection
- Warm air dry blowing function
- Increasing payload capacity up to 1,500kg
- Rinse function via direct water supply line
- Automatic cleaning programs
- Oil filter (settling tank)
- Hour meter
ProSonic builds and installs machines in all markets!
The sectors in which our customers operate are incredibly broad. As a result, our knowledge has become very extensive. Whether it's cleaners in clean rooms or heavy duty cleaners that are outside daily in refineries. We are there for every application.
Automotive industry

The Automotive series is specially designed for cleaning and degreasing all types of parts and components in the automotive industry. It achieves excellent cleaning results in many types of materials, especially in complex parts, where our ultrasound produces excellent results thanks to our 28Khz digital synchronized generators.
Industrial motors

The large diesel engine industry requires the same specification as the automotive sector, but with a few exceptions, everything is bigger, more robust and a tad more polluted. also for this we have the larger ultrasonic cleaners with unprecedented cavitation power!
Injection molds

Our method for cleaning molds completely removes all residual release agents, oils, greases and materials, such as zamak, aluminum, brass or any type of carbonized plastic or rubber.
Food Industry

ProSonic ultrasonic cleaning equipment not only removes (charred) food residues, but also eliminates microbiological hazards, achieving the best hygiene and safety in the can.
Cleaning in cleanrooms

High end wet surface cleaning, from simple stand alone baths to complex and larger multistage baths and from physical transport automating to datalog systems that work together with you log systems. we offer it to you under one roof.
Discharge

The aggressiveness of our cavitation can make it necessary to work with less violent paint strip chemicals. In fact, you process will get a boost and much more work will be done in a day!
Metalworking

During metal machining, a lot of cool and cutting fluids are used. After machining, these fluids can attract ugly in the new surface structure of the part. To prevent this, direct ultrasonic cleaning is the solution.
Medicinal cleansing

Ultrasonic cavitation kills microorganisms by breaking the cell wall. In conjunction with proper chemicals and a high temperature, it is a powerful formula to kill bacteria such as enterobacteriaceae, Salmonella, Listeria monocytogenes or even Brettanomyces.
Shipping

Equipment from ProSonic is the optimal solution for cleaning any marine element or parts of energy production facilities. Our customized equipment is designed for professional use on board!
Aviation industry

Our exclusive technology is ideal for cleaning hydraulic systems, engine components, injection pumps, vanes and turbines. critical products can be cleaned under monitoring digital data logging.
Printing

No matter how peculiar your printing system may be, and regardless of the quality and printing inks used, ProSonic offers a cleaning solution that breathes new life into your anilox printing rollers. Colors come back to life like never before!
Industrial maintenance
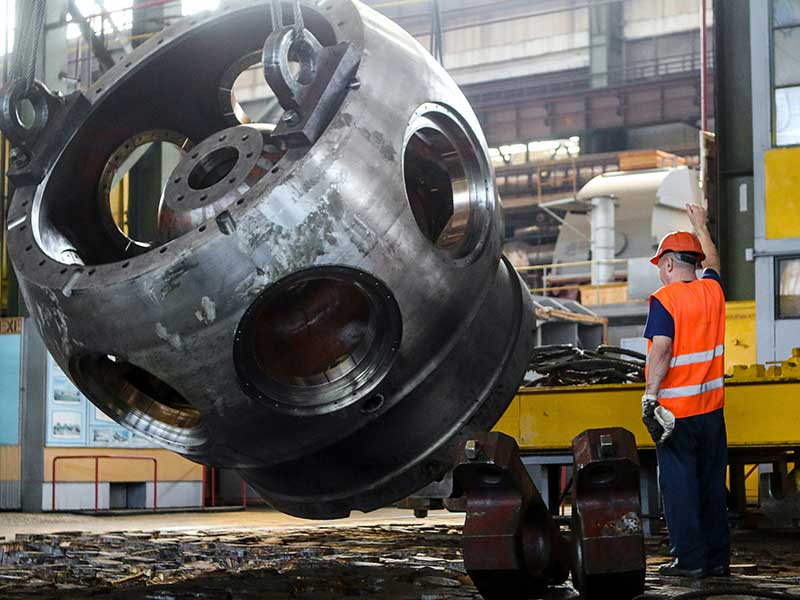
Whether the maintenance is periodic or corrective, the overhaul of parts will have to be done. That is why our industrial line has been developed to always give reliable and desired results.
Automated lines
A subject whose heart beats faster: Automation.
In many processes, the same (type of) part often needs to be cleaned. We can then use various tests to find out under which parameters we can best clean the product/part. This often involves factors such as: ultrasonic power, frequency, chemicals, temperature, cycle time, rinsing, drying, etc. Once everything has been defined, we can design and implement machines that function fully or semi-automatically. By means of various sensors and filter systems we keep a close eye on the quality of the liquid so that production cleaners can run 24/7.
Transporting the parts through the line can be accomplished by overhead crane, robotic arms or conveyor systems.

Projects completed by ProSonic
Marine Maintenance industry

The machine on the left is specially designed
Industrial heat exchangers

The bigger the better, 2 stage 30,000L
Automated rim cleaning
